Remote and automated power line inspection
The energy industry still has difficulty grasping the fact that airborne inspection with drones can be implemented on a commercial level to prevent power line failures through remote inspection and automated power line analysis. For this reason, we would like to delve deeper into details considering power line inspection technology, especially UAV payloads and software, that occupies an extensive place in power line data gathering and analysis.
The reliance on drones to ensure the security of power supply facilities has increased. Therefore, the market for drones in the power and utility industry will continue to broaden with an annual growth rate of 23.6%, reaching $515 million by 2030.
Currently, around 60%–70% of grid inspection can be automated, and this number will likely grow significantly in the coming years. Drone-based power line inspection shortens inspection cycles, provides more accurate defect detection, and, most importantly, reveals potential power line damages. Apart from nullifying safety risks, drones minimise the need to send people on-site to be deployed for monitoring, operations, and maintenance services.
Variety of UAV payloads to gather data
Hepta’s innovations always focus on payloads to ensure that the drones cover the required inspection areas and succeed in efficient data gathering.
The company currently uses various payloads – including optical RGB photos, infrared, LiDAR, and CORONA – to gather the data required by grid operators.
Depending on the mission and type of aircraft, single- or multiple-sensor payloads can be attached to the drone. The cameras used in the inspection are optical – capturing RGB images in the colour’s orange, red, green, and blue – and range from 42- to 115-megapixel resolution.
LiDAR
Hepta is extensively working with LiDARs as there is great potential in getting a full 3D view of the assets and the analysis thereof. While some earlier LiDAR tests were performed using fixed-wing aircraft, soon, Hepta found that LiDAR functions best when on-board a UAV helicopter.
For northern countries, LiDAR is especially important as it allows for a rapid response in harsh and dark weather conditions 24/7. Hepta helicopters equipped with LiDAR payloads might be the only ones to gather data to support relief work as autonomous helicopter drones can quickly continue work around the clock.
LiDAR works similarly to radar yet uses light waves from a laser instead of radio waves. A LiDAR system calculates how long it takes for light to hit an object or surface and reflect back to the scanner. LiDAR data is used to create an accurate 3D model of the surroundings. It allows the creation of point clouds with 2–5 cm accuracy, which can be compared later with physical measurements. For vegetation, the difference is typically around 10 cm, which is considered to be accurate. LiDAR captures exact data; however, the level of precision depends on the mission. Some missions do not need super-precise data, but for those who need extreme accuracy, it is not uncommon to do several flyovers to capture the necessary level of detail.
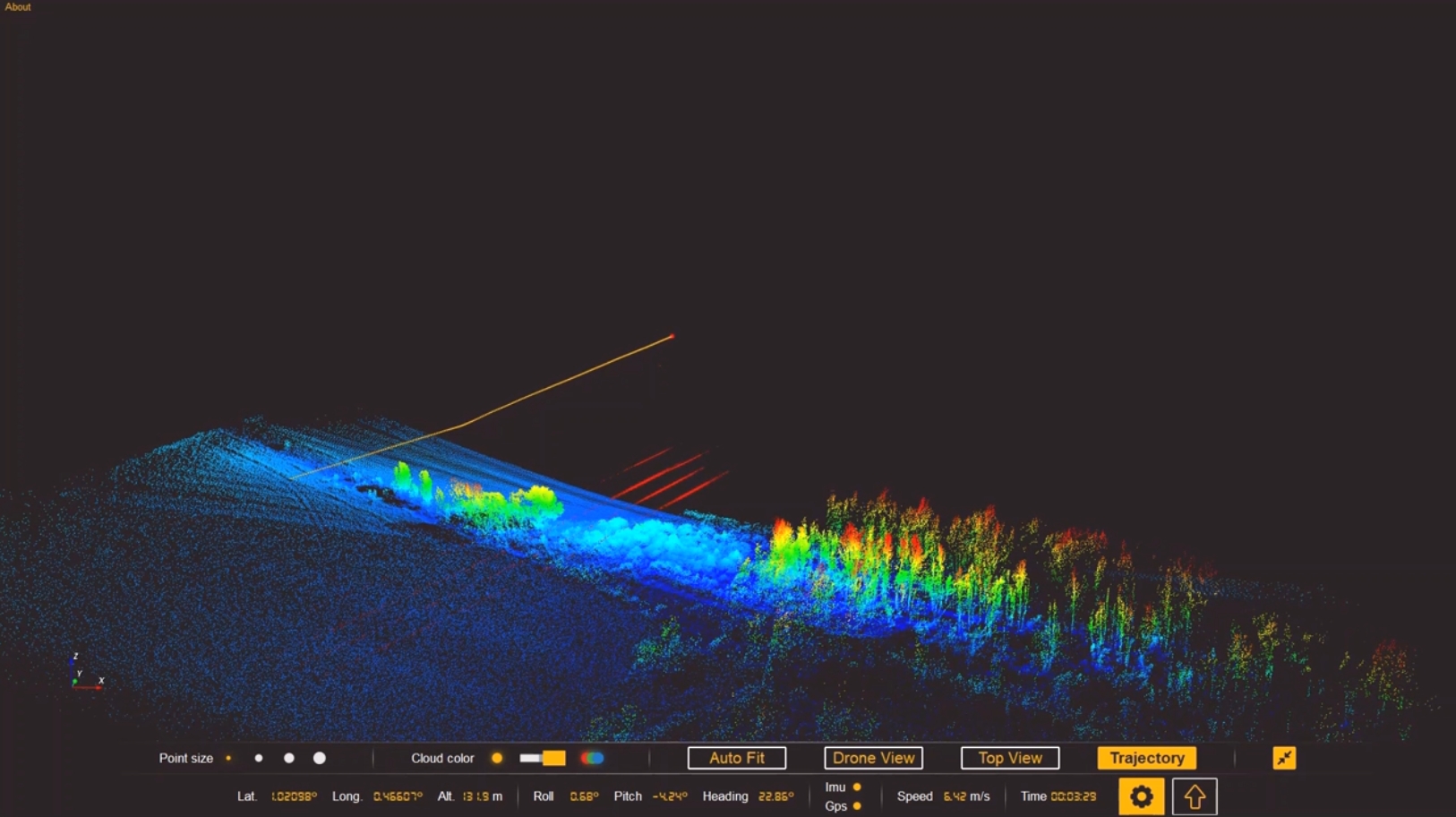
LiDAR point cloud animation of power lines and vegetation- birds-eye view.
Thermal camera
The other type of camera that is often used is the infrared or thermal camera. It measures the temperature of any surface as it detects the different light waves reflected from the elements depending on the surface temperature. The infrared camera can measure the temperature of power lines, insulators, and surroundings and, based on technical specs, allows the detection of heat and decides whether the defect is severe enough to take action or not.
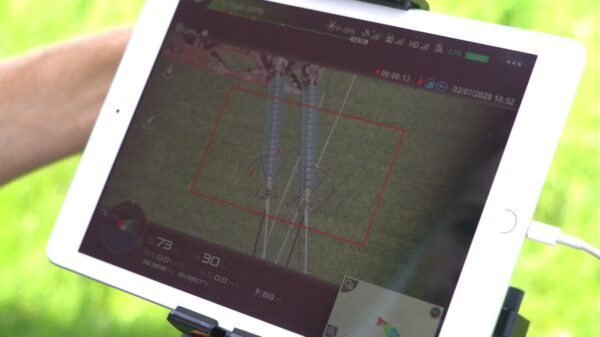
Corona discharge effect on high voltage power lines.
CORONA
The third payload used is called the CORONA HD camera, with dual sensors, UV and visible, capable of detecting and imaging corona in daylight. It instantly maps UV data on a video stream. Compared with other devices of the same class, CORONA provides a more comprehensive (up to one hundred times) dynamic range, has better (more than ten times) UV angle resolution, and has a noticeably greater signal-to-noise ratio (SNR). It is highly effective on power lines. Corona occurs at 35 kV and above, where high local electrical field strength ionises the air, resulting in power losses, ozone and nitric acid formation, audible noise, RF interference, and UV emissions – all of which are destructive to the infrastructure and surrounding equipment. The UV emissions can be visualised with the device, and while this is a new addition to the market, it is quickly developing and gaining popularity among professionals.
The pairing of UAV hardware and UAV payload
The best pairing of hardware and payload is required to achieve high-quality results, which can only be ensured by an expert with extensive experience working with various aircraft and payloads. In a mission to produce optimal hardware for aerial power line inspection, Hepta has undergone three stages: the fixed-wing drone, the multi-rotor aircraft, and the unmanned helicopter aircraft. Finally, Hepta has developed an in-house aircraft suitable for power line inspection both in small areas and for long distances. The use of optimal UAV payloads has significantly contributed to the process of producing helicopter aircraft.
Software as a data analysis tool
The last leg of inspection is analysing the gathered data. Hepta Insights is the first end-to-end power line inspection software. The solution uses high-end tech to automate the data analysis of power lines and enables the digitalisation of the whole grid infrastructure on a large scale.
The Hepta Insights platform can process optical (RGB) photos and use machine learning to identify the most common defects. Inspections can also be performed manually, identify faults, and produce reports in many different formats: online in the cloud, CSV tables, Excel tables, and PDF reports, depending on the customer’s needs. Most standard output formats are PDFs; reports of the defects can be printed and customised to ease the work of line technicians. Hepta Insights can be integrated with almost any other system, and for one of our customers, it has been integrated with SAP.
Requirements of the commercial-grade of power line inspection service
Effective and automated airborne inspection requires a set of competencies which grid operators usually lack. A successful operator needs to be advanced in multiple disciplines: UAVs, UAV payloads, software and data processing, operational models, and airspace regulation.
Given such complexity, very few companies have found out how to deliver a service that meets commercial use requirements.
To get a further understanding of how Hepta methodology provides commercially viable power line inspection and analysis, register below to read the eBook “Mastering efficient power line inspection: What energy companies need to know”.